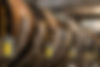
Dyeing
The dyeing of the leather takes place between the tanning phase and the finishing phase: colours, reflections and shades are the result of great skill, technological innovation and precise stylistic choices. To produce an excellent quality and evenly dyed leather product requires a lot of experience and an integrated and environmentally friendly approach based on zero waste concepts.
The dyeing is carried out in specific drums and can be divided into three distinct phases which improve the aesthetic characteristics of the leather: the re-tanning, the fatliquoring and the actual dyeing. Re-tanning allows to giving the leather adequate fullness. This is followed by the fattening, carried out with oils and fats of natural or synthetic origin, which has the aim of improving the degree of softness of the leather, giving it various characteristics, including impermeability, resistance to wear and tear, and elasticity. Finally, the actual dyeing is the operation by which the surface or section of the chosen leather is colored. To create a truly unique and valuable product, we have a sophisticated automated system for monitoring, dosing and checking the entire dyeing process which operates under the strict control of our qualified personnel. The dyed leathers are subsequently subjected to the delicate conditioning process, necessary to rehydrate the leather, through different techniques, such as vacuum, loom or dry spinning. Once dried, the leather, known by the term "crust", is ready to be finished.
Specifically, the department is equipped with:
-
10 wooden drums of different capacities (from 700 kg to 1,800 kg each) with a production capacity of around 900/1000kg/day;
-
3 sampling mini drums;
-
a sophisticated automated system for monitoring, dosing and controlling the dyeing process, always combined with rigorous in-line control by specialized operators.